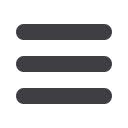
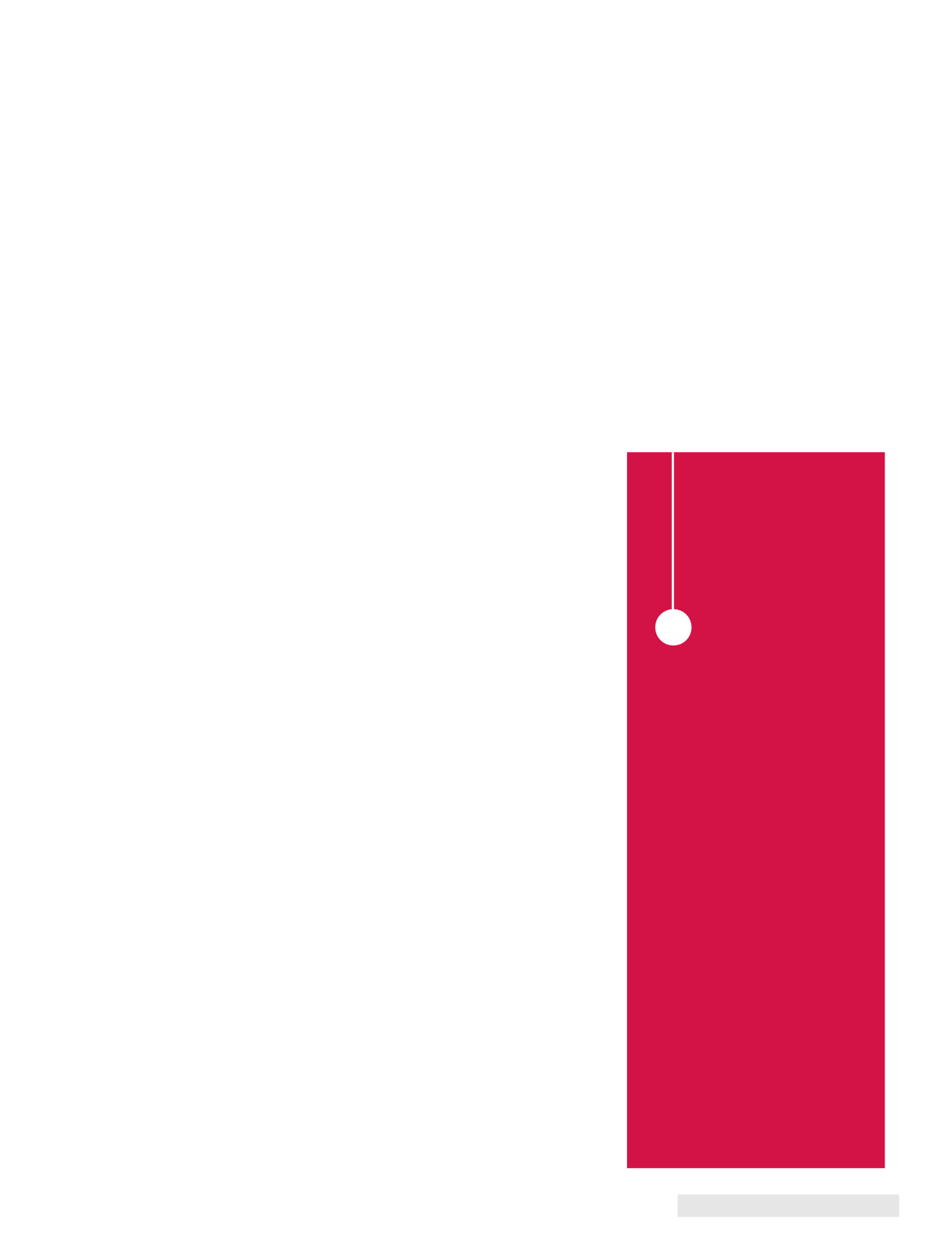
Business Worl d Magazine
The lighter the vehicle, the longer its
range. According to Ducker Worldwide,
aluminum is expected to contribute
more than half of the anticipated
vehicle mass reduction demanded by
electric vehicles (EVs) to extend range.
Ducker reports that in North America
alone, aluminum content in EVs will
increase to nearly 565 pounds (256
kilgrams) per vehicle by 2028.
The larger the vehicle, the heavier the
battery and casing required to optimize
the EV’s range. It is the larger EVs, i.e.,
sedans, SUVs, taxis, trucks and buses,
that will realize the greatest benefits
from a steel-to-aluminum conversion.
In the U.S., a vehicle’s gross weight
determines which class of commercial
driver’s license (CDL) will be required.
Without lightweighting, some EVs could
demand a higher-class license or addi-
tional endorsements due to the added
weight of the battery. In older Europe-
an cities like Brussels or London, some
bridges and tunnels only allow vehicles
up to 3.5 tons in weight, a target that
is very difficult to meet for larger EVs
without lightweighting.
For heavier material transport EVs such
as trucks, weight reduction enables an
increased payload, providing a signifi-
cant monetary benefit. Generally, the
larger the vehicle,
the higher the payback.
Particularly relevant for larger human
transport EVs such as buses and taxis,
the weight reduction made possible
through aluminum provides the added
benefit of reduced CO2 emissions and
improved air quality, of value not only
to vehicle operators, but to the commu-
nities they serve.
The thermal and anti-corrosion proper-
ties of aluminum make it ideal for bat-
tery frames. Sea-water resistant, highly
formable, highly surfaced aluminum
alloys provide the strength necessary
to pass side-impact crashworthiness
testing, protecting passengers and the
battery should impact occur. Casing
floor plates made out of aluminum are
not only strong, but also capable of
resisting corrosion related to weather
exposure. These characteristics enable
aluminum battery casings to resist
weather-related deterioration and im-
pact from road debris, minimizing the
risk of related fires and further securing
passenger safety.
Optimizing battery and
human safety
Extending range
Dispersing heat
The batteries used in EVs produce
energy while charging and decharging,
requiring the use of heat exchangers
to dissipate heat. But the types of heat
exchangers used in vehicle air condi-
tioning systems are inadequate to meet
this new challenge.
Aluminum clad brazing (which connects
multiple layers of aluminum together
to disperse heat) requires heating in a
controlled atmosphere (e.g., a vacuum)
to achieve optimum joining. Aluminum
heat exchangers designed specifically
to meet the challenges presented by
electric vehicles can use as many as five
types of aluminum sandwiched togeth-
er, with the layers providing gradient
properties to optimize cooling.
These specialized processes and ma-
terials address OEM concerns, ensur-
ing adequate dissipation of the heat
generated by battery-powered vehicles.
An experienced aluminum processing
partner can help OEMs specify the right
process and alloys to meet specific
vehicle temperature thresholds, ideally
working side by side with OEM engi-
neers early in the design process to
maximize the performance of electric
vehicles.
IT IS THE LARGER EVS,
I.E, SEDANS, SUVS,
TAXIS, TRUCKS AND
BUSES, THAT WILL
REALIZE THE GREATEST
BENEFITS FROM A
STEEL -TO-ALUMINUM
CONVERSION .