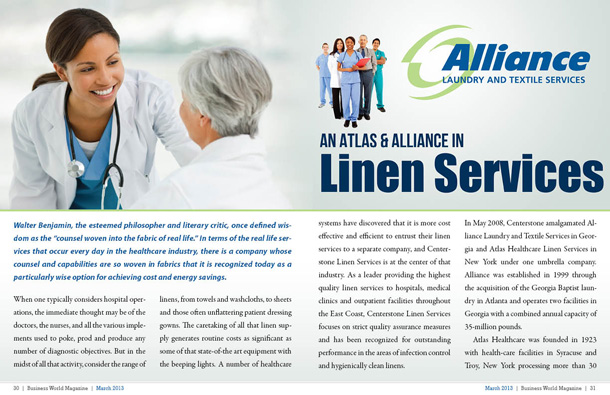
An Atlas & Alliance in Linen Services.
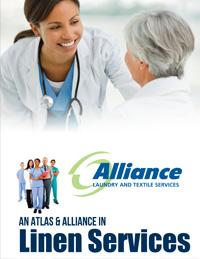
Walter Benjamin, the esteemed philosopher and literary critic, once defined wisdom as the “counsel woven into the fabric of real life.†In terms of the real life services that occur every day in the healthcare industry, there is a company whose counsel and capabilities are so woven in fabrics that it is recognized today as a particularly wise option for achieving cost and energy savings.Â
When one typically considers hospital operations, the immediate thought may be of the doctors, the nurses, and all the various implements used to poke, prod and produce any number of diagnostic objectives. But in the midst of all that activity, consider the range of linens, from towels and washcloths, to sheets and those often unflattering patient dressing gowns. The caretaking of all that linen supply generates routine costs as significant as some of that state-of-the art equipment with the beeping lights.
A number of healthcare systems have discovered that it is more cost effective and efficient to entrust their linen services to a separate company, and Centerstone Linen Services is at the center of that industry. As a leader providing the highest quality linen services to hospitals, medical clinics and outpatient facilities throughout the East Coast, Centerstone Linen Services focuses on strict quality assurance measures and has been recognized for outstanding performance in the areas of infection control and hygienically clean linens.
In May 2008, Centerstone amalgamated Alliance Laundry and Textile Services in Georgia and Atlas Healthcare Linen Services in New York under one umbrella company. Alliance was established in 1999 through the acquisition of the Georgia Baptist laundry in Atlanta and operates two facilities in Georgia with a combined annual capacity of 35-million pounds.
Atlas Healthcare was founded in 1923 with health-care facilities in Syracuse and Troy, New York processing more than 30 million pounds annually. Atlas also operated a special services facility for medical clinics and a surgical linen pack room that includes sterilization.
“From his law practice in Buffalo, New York, John Giardino was behind that and had been working with a number of local hospitals in the Buffalo area. He was asked to look for a development solution to their problems with aging in-house laundries that were expensive to operate and in need of significant capital improvement dollars,†says Centerstone COO Ron Seaman, who joined the company in 2008.
Since their inception, Centerstone has opened new facilities in Austell, Georgia, Winchester, Tennessee, and Pittsburgh, Pennsylvania, and is soon poised to open a third New York State health-care facility in Buffalo.  “There has also been significant organic growth with additional volumes being incorporated into the existing facilities,†says Seaman.
Health-care focus
While many laundry production facilities produce work for various industries such as healthcare, hospitality and uniform rental businesses, Centerstone Linen Services has a sole focus on health-care linen rental as its primary business model. Â This primary focus on health-care linen allows them to provide attention to detail and quality to every product that comes out their facilities.
To ensure quality, every facility is certified through the Healthcare Laundry Accreditation Council (HLAC), which requires participating companies to adhere to safety and operating standards designed to protect the staff within the laundries and hospitals, and the patients they serve. “The HLAC accreditation standards cover many aspects of a health-care laundry processing operation – from the use of personal protective clothing to the maintaining of employee training records as required by OSHA,†Seaman says.
In terms of safety, Centerstone recently promoted Andrea Bessel to corporate safety director. She’s been instrumental in raising safety awareness through monthly conference calls with all plant managers, as well as having monthly site-inspections bringing best practices to each facility. “The use of puncture resistant gloves for all soiled sorting staff has prevented any soiled sorting associate from being stuck with a needle left in the soiled linen,†he says.
Another advantage to choosing Centerstone is their IT platform, which is far superior to their competitors, Seaman explains, adding they’re very advanced technologically in their industry. It is used for billing, as well as an effective linen management software program helping hospitals efficiently manage their linen utilization and costs.
“We provide a lot of reports and data for our customers, whereas nobody else does,†he says. “We do more than just the laundry – we are truly a linen management organization.â€
Apart of that linen management is exchange carts that have pre-determined quotas of linens set up in pars for each unit within a hospital. The quotas of linen items are designed to last for a specific period of time, which is usually 24 hours. Each day, the depleted cart is removed from the nursing unit and replaced with a new cart with the full quota. This unique process is a service their competitors can’t match in terms of quality, Seaman says.
“The program calculates the number of various linen items required bringing the cart up to its established quota and a pick ticket is printed and placed on the cart so the linen staff may refill the cart ready for delivery the next day.â€
Centerstone processes and delivers more than 420,000 pieces of linen each day, making them an integral part of their customers supply chain. To ensure an efficient production flow, chemicals, packaging supplies and maintenance parts are paired together with sufficient supplies of linens and a fleet of 50 trucks to ensure daily on-time deliveries. Â Centerstone requires effective partnerships with their suppliers as a prime business imperative, Seaman explains.
The company instills a corporate culture based on providing excellent customer service and the development of a safe environment for their associates and more than 700 employees that serve 600-plus customers. An example of their personalized service involved a patient’s lost ring approximately two years ago, which wasn’t found at the time.
“Recently one of our maintenance associates happened to come across the ring while working on a washer and was engraved with a name,†he says. “After some research, the facility manager located the owner and returned the ring back to the owner.â€
Continued success
At the moment, Centerstone Linen Services is in a bid to buy a plant in South Carolina, which would add 120 employees to their ranks in the not-too-distant future. “By next year we could be at more than 1,000 employees,†Seaman says.  They also expect to have their first fully-functioning ceramic and Nano filter system in place by early 2014.
Looking ahead to the longer term, Centerstone will continue to evolve and proudly serve the health-care market with quality linen items in the southeast and upper-Midwest states. “We want to continually differentiate ourselves by having customers gladly recommend us while creating a highly professional, lean, customer-focused management team that is rewarded through shared performance,†he says.
Preferred Vendors of Choice: