
Consolidated Capability
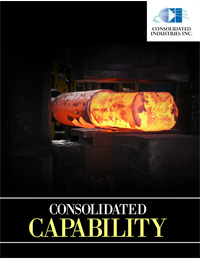
“Nothing splendid was ever created in cold blood … heat is required to forge anything,†observed Author Arnold Glasgow, who further noted, “Every great accomplishment is the story of a flaming heart.†And when it comes to the story of a Connecticut-based metal forging enterprise, the splendid accomplishments wrought over the last sixty years have been fueled, indeed, by a burning passion to serve, and more often than not, that service is critical to those who serve and protect our nation.
Over the last six decades, incredible advancements have been achieved in the designing and engineering of aeronautics, be it in the form of fixed-wing aircraft and jet engines to helicopters, nuclear propulsion systems and more. The emergence of such mechanized marvels has been supported by the vital efforts and expertise of a dynamic metal forging company known as Consolidated Industries. Operating from a 15-acre site in Cheshire, Connecticut, Consolidated Industries is a producer of custom-designed, closed-and-open varieties of die forgings essential in the manufacturing of some of the world’s most sophisticated technical innovations. Consolidated Industries’ components can be found among the applications on Sikorsky “Blackhawk†and Boeing “Chinook†helicopters, Lockheed’s C-130 “Hercules†and Northrop Grumman’s E-2C “Hawkeye†– just a few examples of their highflying handiwork. Consolidated produces fuel system valves, as well as the elbows, blades and vanes for aircraft engines. They forge the shafts, fins, adapter collars and controllers utilized in missiles. They make the rotor components for helicopters, the landing gear components in aircraft frames and the stainless steel blades and vanes necessary for the generation of power. The client list of Consolidated reads like a Who’s Who of the defense industry, including such powers as Raytheon, United Technologies, Woodward and Lord Corporation. Vice President of Business Development Roger Briggs says the masters of metal forging at Consolidated exact extra-special attention to detail because they’re fully cognizant of the applications in which their components serve. He also says his team revels in a certain pride born from their unique support to the defense industry. “Nothing thrills our team more than seeing how our forgings are being applied in aircraft… our employees appreciate being able to help the troops who help keep our world safe. That makes them take their job very serious, but it also makes them feel very proud too,†says Briggs.
Evolving Efficiency
When it was established in 1948, Consolidated was initially tasked with serving interests in agriculture, particularly by providing components for tractors, which stands to reason since its home community, Cheshire, has enjoyed historic distinction as the leading capitol of bedding plants in the state of Connecticut. A small family-owned enterprise, Consolidated prospered by serving larger companies that were expanding their own respective product lines and service offerings. The growth of Pratt & Whitney, for example, contributed to the growth of Consolidated. Another significant development occurred when the ship building company of Newport News determined to cease its in-house forging operations and outsourced the job to Consolidated. In fulfilling demand for these major accounts, Consolidated routinely invested in new equipment and further expanded its capabilities, all along growing its reputation as an integral partner in the supply chain of leading manufacturers.
The company endured through eras of varied corporate ownership before a leveraged buy-out saw it acquired by a team of financiers collaborating as the Consolidated Industries Acquisition Group. This occurred in 1999 and the new CEO, John Wilbur, instinctively realized that for Consolidated to move beyond the new millennium, the company would have to be more aggressive in securing new clients. Over the next decade of his leadership, annual sales went from $8 million to more than $30 million.  Business planning, performance monitoring & measuring, and the demanding drive to achieve objectives would prove significant to advancing Consolidated Industries over the years that followed. Staff development was equally important in the process. “We’ve always strived to bring in the most highly trained, technically-skilled people,†says Briggs, noting that beyond the various degreed employees working at Consolidated, there is also what he describes as “high-tech blacksmiths.†Briggs says Consolidated doesn’t simply rely on schools to do the job; it conducts its own system of schooling, and views training and staff development as a vital part of their own operations.
In connecting, honing and building upon skill sets, Consolidated significantly expanded its capabilities in both design and production. Under Wilbur’s leadership, new product offerings (once limited to six per year) grew to more than seventy per year. At one stage, it was determined that as much as half of the new products had been co-designed with the customers served by Consolidated. This ability to collaborate, to fully understand the customer requirements and applications for which their forged materials must serve, and actually produce the goods in the quality and time frame demanded, all speaks to the capability of Consolidated Industries. In fact, Briggs notes there has been frequent occasion when Consolidated has examined design specifications and offered alternatives to customers that save them time, money and headache in the long run. This has led to prototypes being delivered in four to six weeks (when industry averages can typically range from 14 to 16 weeks) and components that don’t need to be qualified via the costly ardors of retesting. As engineering consultants, Consolidated offers comprehensive guidance, not only assisting with design and/or redesign, but also metallurgical analysis and design concept to replaced machined hog-outs with more less costly “Near Net Shape†forgings. The company can also provide metal flow analysis when such is dictated as a crucial strength application. The analysis can also be applied to identify failure modes of a machined component and insight as to how an engineered forging could eliminate the problem.
Today, Consolidated Industries is capable of producing forgings in aluminum, stainless steel, alloy steels, magnesium, nickel-base alloys, aluminum-bronze, and all grades of titanium. Titanium forgings can range in weight from .25 pounds to 150 pounds. The company’s efficiencies with steam hammers enable them to produce impression die forging and hand forgings up to 200 pounds in size. Press capabilities include Hydraulic Presses (1500 and 2500Tons), Mechanical Press (1300T), and Cold Trim Presses (150T, 75T, 60T). The company additionally offers partial or full machining services.
Yet, in all cases, Consolidated is committed to continuous improvement consistent with the standards of lean manufacturing principals, standards which complement their expertise with efficiency that adds another benefit to its customers. According to Vice President of Operations Drew Papio, the company has reinvested significantly in the plant throughout the last decade to achieve current capabilities and efficiencies, yet those functions are on the verge of further evolution. Papio indicates that Consolidated is preparing to launch a major plant upgrade which will see several millions of dollars invested in new, state-of-the-art forging and material-handling equipment.
Strategies to build upon the benefits they provide to customers are also integral to operations at Consolidated, especially now, as sequestration factors combined with existing defense budget cuts are anticipated to prompt some weakness in second quarter earnings. Briggs indicates that Consolidated had anticipated the spending cuts sufficiently prior to current factors, and says the company is currently on track for another great year. Consolidated also maintains a healthy client base in automotive, medical device and marine manufacturing, which Briggs anticipates will increase. And while budget cuts may impact certain projects, there is a range of other aircraft that Consolidated will continue to serve. As Briggs says, “The helicopters and the C-130’s will continue to fly.â€
By bringing design, forging and machining operations under one roof, Briggs says Consolidated will build upon the value-added services it is providing to current customers, but he also expects industry consolidation will prompt new services to a new, expanding customer base. Like the best in business, Briggs says Consolidated looks forward to forging new relationships.
By continually developing staff, investing in resources for heightened operational capacity, while monitoring and mandating performance requirements that are consistent with the demands of the critical applications – and clients – who depend on their quality, Consolidated Industries has consolidated resolve to remain a respected leader in its industry.
For more information, please visit their website at: Â Consolidated Industries
i read your blog its very nice blog and videoes it is also pridove us such a good knowledge aboutâ€Video Worthy †I really like it. Thanks to write this blog
Comments are closed.