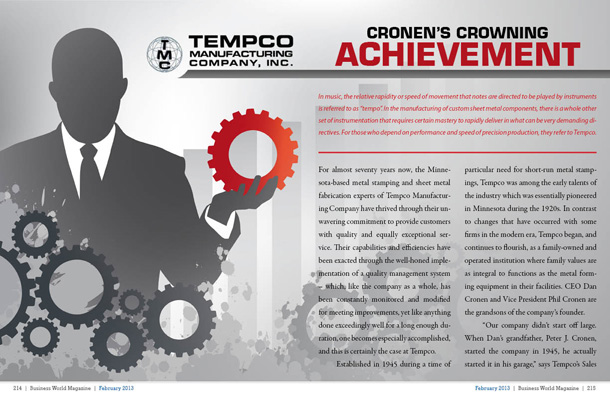
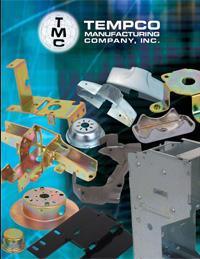
In music, the relative rapidity or speed of movement that notes are directed to be played by instruments is referred to as “tempoâ€. In the manufacturing of custom sheet metal components, there is a whole other set of instrumentation that requires certain mastery to rapidly deliver in what can be very demanding directives. For those who depend on performance and speed of precision production, they refer to Tempco.
For almost seventy years now, the Minnesota-based metal stamping and sheet metal fabrication experts of Tempco Manufacturing Company have thrived through their unwavering commitment to provide customers with quality and equally exceptional service. Their capabilities and efficiencies have been exacted through the well-honed implementation of a quality management system – which, like the company as a whole, has been constantly monitored and modified for meeting improvements, yet like anything done exceedingly well for a long enough duration, one becomes especially accomplished, and this is certainly the case at Tempco.
Established in 1945 during a time of particular need for short-run metal stampings, Tempco was among the early talents of the industry which was essentially pioneered in Minnesota during the 1920s. In contrast to changes that have occurred with some firms in the modern era, Tempco began, and continues to flourish, as a family-owned and operated institution where family values are as integral to functions as the metal forming equipment in their facilities. CEO Dan Cronen and Vice President Phil Cronen are the grandsons of the company’s founder.
“Our company didn’t start off large. When Dan’s grandfather, Peter J. Cronen, started the company in 1945, he actually started it in his garage,†says Tempco’s Sales and Marketing Manager Travis Riesselman. “Now we’re a third generation company that’s firmly instilled in the Cronen family.â€
“There is a lot of family pride in the company and as a result there are people that have been working here 40 or 50 years. There’s a lot of longevity in our company,†he adds.
And where there is that kind of pride in longevity, Riesselman says there is also pride in legacy which equates to committed adherence to the precision standards and moral values which all helped foster Tempco’s reputation as a leader in their industry, not only in terms of yesterday, but here and now.
Industry Integration
Over the years, Tempco Manufacturing Co. Inc. has provided precision metal forming solutions for clients in just about every industry – from the Twin Cities to across the world. The company provides low-cost, top quality stampings, sheet metal fabrications and mechanical assembly services. While growing steadily, they have taken on more than 60,000 different jobs.
“We’re not just tied into one industry – we’re very diverse across lots of different industries. That’s what has kept us strong over the years,†Riesselman says.
Today, Tempco serves a diverse range of clients that make products people use every day. Their customer base includes companies in industries such as: Medical, construction, firearms, fitness equipment, vending machines, door hardware, appliances, light fixtures, dollar bill and coin exchangers, agri-business, aerospace, automotive, locomotive, industrial equipment, computers and electronics.
Over the last few years, the company has seen a spike in the number of their employees due to their growth. Currently, the company employs approximately 135 staff, 30 of which have joined in the last year or two, Riesselman says. All are highly skilled, and most are very experienced at what they do. “Our expert team is trained to handle the most complex of manufacturing challenges for both long and short run precision metal forming projects.â€
To complement their wide range of manufacturing services, Tempco upholds the most rigorous of manufacturing quality control standards. Every project – from precision metal stamping to drilling and tapping – is subjected to their high quality standards. “Quality is definitely a top concern of ours. We’re ISO 9001:2008 certified and we actually just upgraded the registrar that certifies us and conducts annual audits, in an attempt to get even better,†Riesselman says.
Tempco ensures quality assurance in a number of ways, including goals for improving the average set-up time by 80 to 85 percent or better, maintaining rejects below 0.65 percent and improving the average on-time shipping rate to 95 percent or better. They can handle even the toughest of manufacturing challenges, such as deep draw metal stampings, high tolerance sheet metal fabrication, welding and complete mechanical assembly and secondary services.
“As the premier provider of precision metal forming solutions, we handle their toughest manufacturing challenges,†says Riesselman.
In addition, they produce almost all of their tooling and fixtures in-house, which generate considerable cost and time savings to customers in the production of their parts. They do more than just work for them, they also work with them, Riesselman explains. “We address your manufacturing challenges as we would our own, working collaboratively with you to create a value-added relationship,†he says.
Reinvesting in Renewal
Tempco Manufacturing’s modern precision metal forming facilities include more than 125,000 square-feet of production area. This is just one example of the company’s dedication to technology – they are constantly upgrading their equipment to meet the current and future demands of the manufacturing industry.
Every year, Tempco invests at least $1 million in new equipment and training for their employees. With that investment, Tempco has added additional CNC equipment, larger and faster punch presses, welding capabilities, hardware insertion and finishing equipment, among others. Due to their wide range of manufacturing capabilities, they can act as a “One Stop Shop†for their customers. “We want to help them from prototype through production, rather than have them go to one company for prototypes, another for production, and yet another for finishing services,†Riesselman explains.
Tempco’s wide-range of diverse and modern equipment can be used for different shapes, sizes and volumes of parts. For example, they use their waterjet, and CNC equipment for low volumes, and metal stamping equipment for higher volumes; they also have special equipment for miniature parts, as well as other equipment to handle larger and thicker parts up to 12-feet long! Riesselman says. “We’re very flexible and able to meet a lot of our customers’ needs with our diverse equipment.â€
“We try to project where our customers’ needs are going to grow and we try to stay ahead of the curve by our annual acquisitions of newer equipment that is faster, more efficient and automated,†he says. “That helps us stay competitive in our industry and helps our customers succeed in theirs.â€
Moving forward, Riesselman expects the company to maintain their competitive edge by maintaining their growth. On average, the company does about $20 million a year in sales – for 2013, Riesselman estimates they could see an additional $10 million if the manufacturing industry continues to recover, “and we’ll be ready for it!†he says.
Looking ahead to the longer term, Riesselman asserts Tempco will continue that growth, increasing their revenue while continuing to service the needs of their customers. “We’re always in growth mode and we want to keep it that way,†he says. “We also want to keep the customer happy. That’s our #1 priority.â€