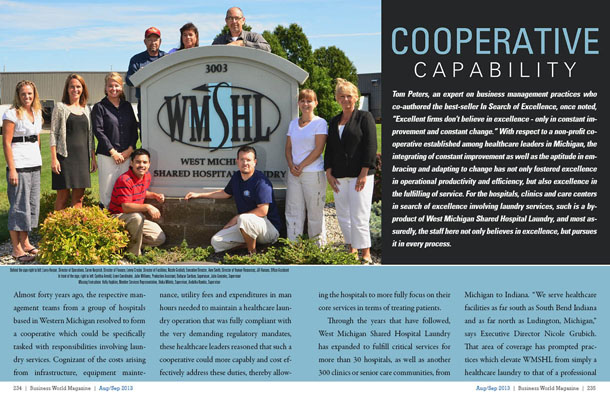
Â
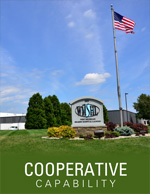
Tom Peters, an expert on business management practices who co-authored the best-seller In Search of Excellence, once noted, “Excellent firms don’t believe in excellence – only in constant improvement and constant change.†With respect to a non-profit cooperative established among healthcare leaders in Michigan, the integrating of constant improvement as well as the aptitude in embracing and adapting to change has not only fostered excellence in operational productivity and efficiency, but also excellence in the fulfilling of service. For the hospitals, clinics and care centers in search of excellence involving laundry services, such is a byproduct of West Michigan Shared Hospital Laundry, and most assuredly, the staff here not only believes in excellence, but pursues it in every process.
Almost forty years ago, the respective management teams from a group of hospitals based in Western Michigan resolved to form a cooperative which could be specifically tasked with responsibilities involving laundry services. Cognizant of the costs arising from infrastructure, equipment maintenance, utility fees and expenditures in man hours needed to maintain a healthcare laundry operation that was fully compliant with the very demanding regulatory mandates, these healthcare leaders reasoned that such a cooperative could more capably and cost effectively address these duties, thereby allowing the hospitals to more fully focus on their core services in terms of treating patients.
Through the years that have followed, West Michigan Shared Hospital Laundry has expanded to fulfill critical services for more than 30 hospitals, as well as another 300 clinics or senior care communities, from Michigan to Indiana. “We serve healthcare facilities as far south as South Bend Indiana and as far north as Ludington, Michigan,†says Executive Director Nicole Grubich. That area of coverage has prompted practices which elevate WMSHL from simply a healthcare laundry to that of a professional logistics company. As Operations Director Larry Harper explains, WMSHL maintains a fleet comprised of vans, semi-tractors and semi-trailers whose daily deployment to some 34 hospitals (along with the weekly or bi-weekly trips to the range of others) ultimately equated to more than 575,000 miles in over-the-road transport of linen last year.  As for its remarkable on-site service capacity, WMSHL annually processes more than 30 million pounds of laundry. “We average 575,000 pounds a week or approximately 160,000 pieces of linen per day,†says Harper.
For all that functionality, these figures only reflect a fraction of WMSHL’s full processing potential, and rest assured, even now the laundry is preparing to take on more work given a recent $14 million investment in a major retrofit of its plant, all accomplished without missing a beat in service to its current customers. While that retrofit resulted in new equipment, new floor space and new efficiencies now helping clients achieve even greater cost savings, WMSHL’s potential to attract new customers won’t simply be an expression of the demand for its services, but demand for the manner in which it fulfills those services.
Eco-Sensitive & Economically Efficient
WMSHL has garnered distinction as one of the most energy-efficient, technologically innovative laundries in the world. To go from great to greater, WMSHL contracted services from American Laundry Systems which specializes in project management solutions vital to the industry. Today, WMSHL is known as a “steamless laundry,†basically, the hot water supply is produced from indirect contact with water heaters as opposed to steam produced from boilers. WMSHL Facilities Director Lenny Crosby says the system not only allows plant operations to start more quickly and conveniently (by not having to wait for a boiler to appropriately heat), but also accommodates up to 40% of savings compared with former utility costs. For that matter, WMSHL was the world’s first laundry to integrate a steamless finishing tunnel, an acquisition achieved through working with a company known as Leonard Automatics. After approaching a number of manufacturers for such a mechanism which had apparently yet to be invented, the laundry found receptive interest by Leonard Automatics and worked with this company to design and manufacture a steamless garment finishing tunnel customized for their plant. As opposed to steam, the system combines processes of hot water and compressed air. Today, WMSHL is one of two known laundries in the world to utilize such a device. Further benefits are found in the utilization of “plate and frame†heat reclamation systems (which heats the incoming supply of water) further add to decreases in utility costs. A ceramic micro-filtration system allows the laundry to reuse water in the wash system which, in turn, diminishes the amount of water consumed while also lowering the costs in terms of what gets discharged to the sewer. The laundry also uses self-contained thermal fluid irons. These devices not only use less energy, but allow for a more tolerant ambient air temperature in the plant, which particularly resonates with laundry personnel.
As a reusable linen healthcare laundry, WMSHL is already more environmentally friendly and economically prudent when compared with the ecological impact and costs arising from those relying on disposable linen. However, WMSHL’s processes are furthered bolstered by best practices in the recycling of plastic bags, water conservation, energy efficiency, and when all the protocols combine, it positions this laundry as a leader in solutions that not only spare impact to the environment, but spare their customers from unnecessary cost.
As for other innovations, WMSHL was among the first in its industry to deploy Jensen’s “Cockpit†production management solution. This technology provides a convenient means of monitoring the status of all mechanical operations in real time. It additionally indicates the activities of operators in every working space, the type of garment or textile being processed, and all manner of data in terms of production time, throughput per machine (per operator and per batch) as well as stats on the consumption of water, steam, gas and electricity.  Crosby says this software package enables data to be accessed through a central location or web portal, to monitor and measure every aspect of plant operations or detect anomalies without having to routinely walk around the plant to physically inspect each apparatus. In addition to saving time, this technology helps WMSHL provide customers details as to the inventory or processing of linen unique to their respective healthcare operations. Crosby says this innovation of technology complements the engineering innovations which WMSHL has consistently sought in its ongoing mission to advance and improve operations. “When I look at our infrastructure, I see a lot of equipment which has serial numbers that are 0001 or 0002, so we’re always looking for ways to be innovative and invest in the cutting-edge technology that helps us perform at our best,†says Crosby.
Let’s Dance
For all the engineering innovations and technological triumphs augmenting operations at WMSHL, Executive Director Grubich emphasizes the laundries “greatest asset,†and in this case, it is not any measure of automated apparatus, but the more than 140 people employed by the laundry. “We can build new machines every day, but this never takes precedence over the relationships we have to build with people … our people are our greatest asset,†says Grubich. Operations Director Harper says a happy and engaged staff is crucial to good quality control and that connotes to happy customers. Good pay, good benefits, consistent communication and welcoming feedback and input by all in morning “huddles†add to an exceptional work environment.
As a healthcare laundry, WMSHL cannot make any compromises with respect to the quality it imparts in the processing of linens. Worker safety and patient safety are too important. Yet at this laundry, the protocols in quality and safety are advanced by directives in dance – yes, dance. As Harper affirms, “I’ve got seventy production people on the floor right now, and if you walk up to any one of them and ask about the dance, they’ll be able to explain it.â€
He goes on to say that “the dance†relates to one’s approach to duty, whether it is the appropriate manner of loading a machine, sorting materials, or inspecting every piece of linen that is processed. “We call that ‘Doing the Dance,’†says Harper. “Instead of me having to harp that you have to inspect every piece of linen and stand over them like Big Brother, we try to make it more fun. “It’s a lot better for my people for me to ask if they’re dancing than to ask if they’re following orders. We also have to realize humans are involved here and you have to find positive ways to interact with each other,†says Harper.
When asked whether there is actual dance while they dance, Harper concedes, “Sometimes I dance more so myself than them, and it is usually quite the sight.â€
Both Grubich and Harper acknowledge that teamwork and team engagement are prime factors of the foundational formula for WMSHL’s success. As Grubich says, “The engagement here is huge. And our directors, managers and even hourly-personnel will affirm that we’re all here for the same reason, to have the highest quality processing and get the product out the door… and everyone here is involved in the process.â€
Accredited Assurance
In terms of the quality imparted in WMSHL processes, the laundry average 270 Quality Checks per day and Harper says that may reflect the highest total of quality inspections undertaken by anyone in the industry. At the same time, WMSHL has been verified as following the industry’s highest standards as reflected by accreditation from the Healthcare Laundry Accreditation Council. In fact, WMSHL achieved accreditation in 2007, one of the earliest in the industry to do so. Earning accreditation involves undergoing a comprehensive audit of all internal operations. Inspectors review mechanical processes, operator procedures involving safety, training and more, and even the manner in which processes are documented and archived. Crosby says the HLAC standards helped the laundry identify areas where record systems could be improved, but with respect to other laundry operations, WMSHL was satisfied to secure more assurance that it was operating responsibly and consistent with the compliance standards mandated by federal regulations. As Grubich explains, “We knew we were already doing the right things, but as a non-profit organization with sixteen owners, this accreditation was an important way to demonstrate that a third party has come in and verified that we’re doing the right thing, which gives our owners greater assurance and confidence in our work.â€
WMSHL is also currently undergoing review by the Textile Rental Services Association that will result in earning certification as a Hygienically Clean laundry, which offers further verification of the quality standards here. Though obtaining such essential industry credentials prompt confidence into WMSHL’s internal operations, the laundry instills assurance in customers through its external operations too. Harper says that means routinely meeting with linen inventory managers from the healthcare facilities served by the laundry, educating them about processes relating to the care of their linens, and involving them in the process of identifying issues or solutions that would lead to improvements in the service. “We’re always looking for ways to make things better for customers,†says Harper. “We talk a lot about the big ‘W’ – the whatever and whenever in what we can do to help…. And part of our job is to educate customers and help them solve problems. We’re all about how to make tomorrow better than today is … and we may not do everything perfect, but we’re trying to.â€
Grubich adds, “Every problem forces a different solution. And sometimes, each hospital thinks that they’re different per se, so they think their needs are different… but across the board, they recognize they’re part of a co-op, and there is a cost-savings and decision-making process as part of a co-op, but at the end of the day, our services all come down to serving patients, and it the satisfaction of patients which really reflects the worth in our services.â€
In terms of the future, Grubich believes there are opportunities to serve more healthcare facilities within its Michigan to Indiana coverage area. Beyond the conventional hospitals and clinics WMSHL has served, Grubich says the future may also include incorporating laundry services involving residential clothing for those who reside in long term, senior care facilities. “We’re looking at that direction and see it as an opportunity to do more for our customers. We look to overcome challenges and we want to grow. Residential clothing services are something new, but we’re looking into that as well as other ways to grow.â€
As it grows, WMSHL will no doubt continue to seek ways to enhance its operations through its continuous improvement program. With only a finite number of things that haven’t been tried, however, Harper says it has grown increasingly difficult to identify “the big wow factor†in terms of what could be improved. By continuing to identify the industry’s greatest offering in cutting-edge technologically and engineering improvements, and by embracing the operational improvements and solutions that drive improvement in the services it provides to its customers; WMSHL has improved its potential for far greater growth and success.
As Harper says, “We still look for ways to improve every day because we truly want to be known as a world class laundry. Some may want to be the biggest laundry, or the most efficient laundry, or the laundry with the smallest carbon footprint, but we want to be world class… we want to be the best.â€
For more information, please visit their website at: Â West Michigan Shared Hospital Laundry
Preferred Vendors of Choice:
- CPI
- American Dawn
- Cromwell Textile
- Universal Laundry Machinery
- Jensen
- Action Chemicals