
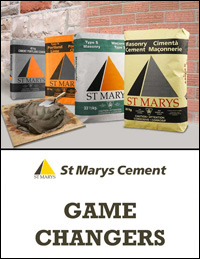
Game changers
For many companies, carbon dioxide (CO2) is one of their most manufactured products, whether they like it or not. At St. Marys Cement Inc, that fact holds true. Instead of simply accepting it, however, they have found a way to turn it into a positive.
Due to a pilot project with Pond Biofuels, St. Marys Cement is able to use algae grown in theirTorontofacility to absorb CO2, and release oxygen in return. The CO2-consuming algae is then continually harvested and can be burned as fuel inside the plant’s cement kiln or processed into biofuels for the company’s truck fleet and biomass for the manufacture of other high-value products. In this manner, St. Marys is producing what is essentially “green cement.â€
St. Marys Cement was founded in 1912 in the eponymous town ofSt. Marys,Ontario. In the 100 years since, they have been a major contributor to the construction industry around the Great Lakes Region, supplying cementitious materials as well as producing concrete and aggregates for theOntariomarket. Today, the company has six manufacturing plants strategically located to serve the Canadian andUnited Statesmarkets, as well as a production capacity of over five million metric tonnes. In the dynamic international business environment, St. Marys Cement also benefits from being a wholly-owned subsidiary of Votorantim Cimentos, an international cement manufacturer based in Sao Paulo, Brazil.
Pond Biofuels, on the other hand, is aTorontostart-up that was founded in May 2007 with the purpose of pursuing biodiesel production from algae. When St. Marys began exploring ideas for reducing C02 emissions from its operations, they happened upon Pond Biofuels by happy coincidence – Donald “Demi†Rogers, former vice-chairman of St. Marys and member of the co-foundingRogersfamily was part of the same shooting club asTerry Graham, chairman of theTorontostart-up. Through them, the two companies began talking. “And that’s how we started going down the road we’re on now with them,†summarises Martin Vroegh, Corporate Environment Manager at St. Marys.
Turning liability into value
Vroegh started full time at St. Marys in 1994, taking over his current position in 2004. After taking on that new role, he immediately looked at a variety of technologies that would address the company’s carbon output. “I was looking for ways to take our second most manufactured product, which is CO2, and find a way to produce value out of it, rather than just letting it be considered an emission,†he says. One of the strategies he considered was the tried and tested method of using heat from their greenhouse gases to grow vegetables (like tomatoes). “However, the reality is that with the mass of volume that comes out of a cement plant you would have as many trucks with tomatoes as you would with cement – so that’s not a very realistic way to sequester carbon.â€
Eventually, Vroegh started hearing about the potential of algae. “But there were no primetime players yet,†he recounts. “Everyone was still playing with beakers and test tubes in the lab; nobody had really done large scale work with it. Because we’re not a research and development firm, or a pure applied research technology company, we wanted to partner with someone who was a little bit further down the road than we could get with the technology.†Shortly after that, Pond Biofuels entered the picture.
At the moment, the Pond Biofuels project is a small model of what a full-scale facility could be. It works by redirecting the plant’s CO2 exhaust through a 15-centimere thick pipe connected to the side of a flue stack. That pipe carries the gas into a facility where a species of algae – harvested from the nearbyThamesRiver– uses a process of photosynthesis to capture the carbon dioxide. The algae are grown in sophisticated bioreactors that are engineered to ensure they achieve the proper balance of light and CO2.
The limestone heated up to create cement is an extremely rich source of carbon dioxide for the algae, which is then processed into biofuels. “Limestone in the cement manufacturing business is 38 per cent carbon dioxide by mass, so when you heat up one tonne limestone, 380 kilograms are going out the smokestack as CO2,†Vroegh says. “It sort of shifts the thinking, actually. The value that can be generated from the CO2 can even be higher than the cement value.â€
Ultimately, both St. Marys and Pond Biofuels see a future where the flue stack stream is diverted to a much larger algae facility.
“A couple of weeks ago, we closed on four and a half million dollars of new funding for the project,†Vroegh says. “Right now we are putting in a 100,000 litre bioreactor tank over the winter.†That tank is significant for the future of the plant and the project. Moving forward, Vroegh says St. Marys will be looking at significantly larger tanks to accommodate the whole size of the plant – and those tanks come in 100,000 litre baffled sections. “That’s because we don’t want to put all of our eggs in one basket, so to speak,†he explains. “If the algae was becoming sick or ill or had some sort of disease in it, we would want to make sure that we could segregate it and not have the entire large scale tank go down. And that’s why 100,000 litres baffled segments are perfect. Introducing this 100,000 litre size means we’re kicking the project up to one of those full size industrial segments.â€
On top of converting the liability of carbon emissions into value, this project will also create green jobs. “One of the interesting things is the technology that Pond Biofuels is putting forward here,†Vroegh says. That technology will not only create jobs in the St. Marys facility, but also jobs working on the type of technology Pond Biofuels is deploying – such as the manufacturing of the parts that go into their bioreactor. “Those include things like the advanced lighting system. Those are a module manufactured unit that would be manufactured inOntarioas an exported green technology.â€
“A small 8,000 litre tank has nearly a dozen lights inside of it,†Vroegh explains. “When you start going up to 100,000 litres and a million litres, you start to get thousands of these lights being required for manufacture. Those lighting systems are not manufactured now, they are just made as almost one-off units – so a manufacturing process would be developed and that would be employing people inOntario.â€
A sustainable commitment
It is important to note that St. Marys’ pilot project with Pond Biofuels is not the only evidence of their commitment to sustainable business practices. Their Bowmanville Cement plant, for instance, is one of the first facilities of any kind inNorth Americato become ISO 50001 certified – which is the new energy management standard. They also have plans to utilise a new category of cement called Contempra™, which was engineered for sustainability purposes specifically. The use of Contempra™ cement in manufacturing concrete decreases CO2 emissions by 10 per cent while still producing concrete with the same level of strength and durability as the concrete produced with regular cement.
Additionally, St. Marys recently completed Ontario’s first alternative fuels testing program that sought to test the viability of non-recyclable residual plastic film from the compost industry as a fuel replacement for petroleum coke in the cement kiln. “This plastic, which is basically plastic grocery bags, is typically thrown into landfills,†Vroegh explains. “We replaced about 23 per cent of our fuel supply with this polyethylene plastic film, which would otherwise go to landfill.â€
That initiative reduced the carbon content of that substituted fuel from roughly 92 to 74 per cent. “We completed those trials in May very successfully,†Vroegh continues. “It resulted in a decrease in carbon emissions, and overall there’s no adverse effect or impact on any of the environmental emissions whatsoever.†In the long term, St Marys plans to continue those efforts to recover energy from resources that would otherwise get thrown in the garbage. The alternative, after all, is that those resources decompose in landfills, a process that produces methane gas – which is 21 times more powerful at warming the atmosphere than carbon dioxide.
St Marys’ environmental stance goes right to the core of their business. “When we look at the type of projects that our products are involved with, we see they’re all green buildings,†Vroegh says. “We see that our customers are demanding greener building materials. We see the way of the future is to make sure we’re producing some of the greenest cement and cementitious products that the market can have.â€
A game changing future
Moving forward, Vroegh sees St Marys continuing to innovate in the realm of sustainability. He sees the Pond Biofuels project growing to uncharted heights and even changing the way people think of greenhouse gas. “In the next 18 months or so we hope to complete the engineering and start on a full implementation of the algae project,†he says. “We want to be taking steps to a near-zero greenhouse gas cement plant. Since concrete is such a long lasting and sustainable building product we see the way of the future is to make sure we’re producing the greenest cements and cementitious products possible.â€
“And a near-zero emission cement plant – that changes everything,†Vroegh continues. “That’s a complete game changer on greenhouse gas. It basically sets the new standard, and almost makes any discussions on carbon markets irrelevant. When greenhouse gas can be converted into a commodity, it raises the question of how a cap and trade market could even function or exist. Why would people want to be disposing of a product that has value?â€