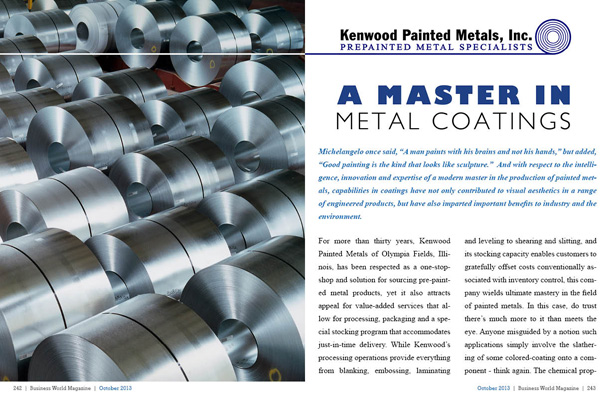
A Master in Metal Coatings
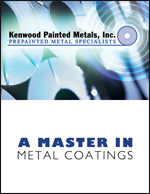
Michelangelo once said, “A man paints with his brains and not his hands,†but added, “Good painting is the kind that looks like sculpture.â€Â And with respect to the intelligence, innovation and expertise of a modern master in the production of painted metals, capabilities in coatings have not only contributed to visual aesthetics in a range of engineered products, but have also imparted important benefits to industry and the environment.
For more than thirty years, Kenwood Painted Metals of Olympia Fields, Illinois, has been respected as a one-stop-shop and solution for sourcing pre-painted metal products, yet it also attracts appeal for value-added services that allow for processing, packaging and a special stocking program that accommodates just-in-time delivery. While Kenwood’s processing operations provide everything from blanking, embossing, laminating and leveling to shearing and slitting, and its stocking capacity enables customers to gratefully offset costs conventionally associated with inventory control, this company wields ultimate mastery in the field of painted metals. In this case, do trust there’s much more to it than meets the eye. Anyone misguided by a notion such applications simply involve the slathering of some colored-coating onto a component – think again. The chemical properties, compositional structure and even the method in which a coating is applied imparts qualities that involve much more than shades of color, but connote to shades of greatness in attributes that augment the integrity, durability and functional character of the material that is being coated. There’s a lot of science and sophisticated engineering that contributes to any coating, and with respect to the innovations coming from Kenwood, the science and engineering also offers benefits in cost-effectiveness, convenience and care for the environment.
To put all of that in proper perspective requires some insight from Greg Underwood, a paint chemist and industry pioneer that left off from a family legacy at U.S. Steel to launch a new legacy with the founding of Kenwood Painted Metals in 1983. “The chemistry involved in creating paint and special coatings … so much of that is taken for granted by our competitors, but our understanding and appreciation for the range of innovations and applications helps distinguish our company from others,†says Underwood. Yet, to be sure, the same could be said for what separates Underwood from others. At U.S. Steel, Underwood was on the front line of developing new paint technology. He was involved in formulating new coatings that led to the effective bonding of paint to galvanized steel; processes which spurred applications like the silver metallic coating used on windshield wiper blades sold by the industry dynamo known as ANCO. Those windshield wipers went on to be sold throughout the world, but Underwood was a key player in developing the coatings used for these materials, and more.
As opposed to paint, Underwood will more readily acknowledge that steel is in his blood. His father worked at U.S. Steel as well as his Grandfather. As a third generation employee who held a good position in the company’s steel supply division, there was more than mild disbelief when Underwood told his family about his plans to start his own enterprise. “My father said, ‘You’re going to do WHAT?’†recalls Underwood. As it was, Marathon Oil had just acquired U.S. Steel’s supply division during this time. With questions as to the changes that might portend, coupled with his sense of potential business opportunities, Underwood set out to create his own company and partnered with a man named Ken Stevens (the same man who had served as his direct supervisor at U.S. Steel). Kenwood Painted Metals was started on a shoe-string budget in 1983 and some of its first customers were former U.S. Steel clients who had come to trust and value working with Underwood.
Kenwood flourished for providing a “one order, one source, one invoice†solution, says Underwood. This means clients not only access any kind of coating they need, but secure processing and inventory stocking services too. “Customers appreciate that we carry their inventory,†explains Underwood. “ That means we’re carrying financial responsibility for that inventory … We try to run a ninety day supply and we’ll carry the burden of the inventory, stock it at different locations across the country and customers only pay for the portion they want released. We put the investment up front ourselves … to get the steel, get it painted, get it processed, and ready to ship to them as their just in time needs arise.â€
 Today, Kenwood Painted Metals has evolved to supply goods for a range of industries. From automotive parts and accessories for the transportation industry and appliances, office furniture and HVAC systems in the consumer market to the lighting fixtures, roofing, exterior walls and doors used in the construction field, Kenwood’s coatings cover a significant swath of industry sectors throughout America. When watching the opening/closing of an electronic-controlled garage door, or when seeing the skirting that surrounds a mobile home, or when looking up at the white metal canopy that covers the gas pumps at a service station, there’s a good chance you’re seeing the handiwork of Kenwood Painted Metals. As Underwood explains, “We align the coating for the particular application… all paints have different properties of varying flexibility or hardness. There are many variables that go into making a whole paint system. Some coatings have to be able to move with the metal while others have to specially withstand environmental impacts… part of our success comes from understanding which coating works best for each application.â€
Conscientious Coiler
Beyond its knowledge and expertise, Kenwood’s market penetration could just as easily stem from the company’s unique approach to service and adherence to methodologies that are as convenient and cost effective as they are environmentally prudent. On the service side of the equation, for all of its growth and market reach, Kenwood functions as a relatively small, family enterprise. Accountability, trust and respect-for-all are values that have been well honed within staff. And while Underwood is a chemist and craftsman, he is also a father who takes great pride in working with his son and step-son who both fulfill important duties at the company. As a family business, greater emphasis is placed in the quality of long time relationships as opposed to quantities in customer interactions. “With some corporate cultures, the customers are treated more like numbers as opposed to people. Every one of our clients knows who we are, and we know who they are too. We value and appreciate their business, as well as their needs, the way only a small business can, and because we’re small, our customers don’t have to jump through a lot of layers to access us when they need.â€
As for its operational advantages, Kenwood specializes in coil coating. In this process, a base metal is unwound, then cleaned and rinsed. After being chemically pretreated, the metal is rinsed again to prepare the surface for coating. A primer is first applied, followed then by a top coat specifically tailored to meet the client’s specifications. The metal can be coated on one or both sides (in the same or different colors), but after each coating, the coil is cured in an oven. Afterwards, the metal is recoiled and ready to be slit to width or cut to length. It can even be rapidly laminated or embossed while it is in its coated-coil form.
Since the application of the paint is precise, it allows for a more controlled film thickness than powder or spray techniques. As only the ideal amount of paint is applied, paint costs are significantly reduced for the client. Time and cost savings are a byproduct of the energy and manpower efficiency inherent in the process. Coil coating lines can run at exceedingly-high speeds, with some operating at 600 to 800 linear feet per minute. While this mitigates bottlenecks that would otherwise emerge from internal finishing operations, it also helps prevent defects in quality. Since the metal is painted while flat (prior to fabrication), the process enables uniform cleaning, pre-treatment, priming, and top coating. Furthermore, as both sides are effectively coated, coil-coating prohibits rusting from the inside out. It ultimately allows for an enhanced appearance, greater product durability and an extended service life.
This same methodology imparts benefits in eco-sensitivity. Since the 1970s, both OSHA and the Environmental Protection Agency have increasingly stepped-up regulatory oversight involving the discharge of waste and pollutants, forcing many manufacturers to either suspend particular operational aspects or invest heavily in infrastructure and manpower in order to maintain environmental compliance. The professional coil coaters that Kenwood employs help eliminate this problem.  They not only deploy special water and air pollution equipment to meets federal, state and local environmental requirements, but coil coating is a closed-loop process in itself. Coil coaters collect volatile organic compounds, control emissions and capture and regenerate solvents; processes that eliminate air and water discharges. Coil coating is the most environmentally friendly process known for applying finishes to metal.
Underwood’s Son Aaron (who manages Kenwood’s Metal Building Division) explains another aspect of the environmentally friendly and energy efficiency provided from special coatings. In recent years, Aaron says the company has expanded its offerings in “cool roof systems.†The roofing and wall panels are coated with a paint that has higher solar reflectivity than conventional paints. This enables building owners to achieve significant savings from reduced utility costs. These materials are Energy Star Certified, and for builders who rely on such advances, the materials also contribute to LEED points consistent with the standards espoused by the U.S. Green Building Council. “Cool roof systems are part of an increasing trend in green building and the Energy Star label has become very important to end users, so we’re happy to work with it,†says Aaron. “Fortunately, there are tax credits available to businesses and homeowners too. If they replace or build using a cool roof methods, tax credits are in place to help offset the costs, so we’re working hand-in-hand with paint suppliers to help market the opportunities and advantages these coatings offer.â€
Kenwood has a long tradition of partnering with industry to promote the advantages inherent in its operational processes as well as helping to clients better understand the scientific advancements which have led to the introduction of new coatings. It maintains a close relationship with many of the major steel mills and paint suppliers, but also trade organizations that include the National Coil Coaters Association, the Door and Access Systems Manufacturers Association and the National Frame Building Association.
“This helps us to stay close to new innovations that come out of these industries, and we don’t see our involvement in term of just selling… we try to stay engaged as an integral member of these organizations too,†says Underwood.
We’ve Got It Covered
In term of the future, Underwood expresses optimism that the company will continue to experience growth as demand for green building materials as well as awareness of new innovative coatings continues to increase. The company has seen markets increasingly embracing new styles of coatings and new laminates that allow metal to have what appears to be a wood-grain finish or printed-pattern. Underwood says customers have style options previously unimagined. He also hints that the company is assisting in the development of new coatings with special chemical properties that will prompt a lot of excitement in the coming soon. Yet, Kenwood’s expertise connotes to a big deal, right now, for the companies it serves. By fully understanding the properties of the materials with which they work, by helping educate others on advancements that impart greater quality and integrity to their respective manufactured goods, and by embracing values that result in greater convenience, customer service, cost savings and care for the environment, this is a company posed for further growth. As for greater success to come, Kenwood Painted Metals has that covered too.
For more information, please visit their website at: Â Â Kenwood Painted Metals
Preferred Vendors of Choice: